クロス穴あけにおけるバリ取りフリー加工
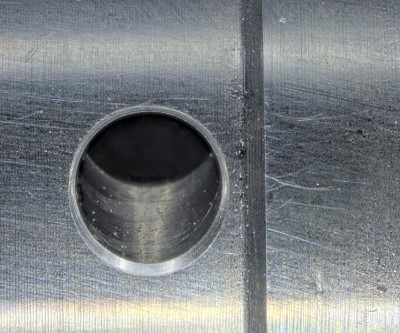
3D機械加工
まず1つ目は、3D機械加工です。特殊刃物を3D加工し、面取りをつけてバリ取りフリーを実現する方法です。
自動機内で完成加工するので、後述する放電加工と比較するとリードタイムが短いです。
ただし、交差穴が大きい(Φ2.5以上)、かつクロス穴の深さが浅い場合(Φ2.5以上)のみ適用可能です。また、アルミなどの快削材なら問題ないですが、ステンレス鋼や高速度工具鋼に対しては厳しい加工方法です。
下図は、A6061の材質にクロス穴Φ2.5でバリ取りフリーを実現した事例です。
細穴放電加工
2つ目は、細穴放電加工です。細穴専用全数自動検査付の放電加工機にてクロス穴を加工する方法です。
材質が導電性で、クロス穴のサイズがΦ1.5~2.0の際に適用できます。また、貫通穴がある方が加工しやすいです。3D機械加工と比較し、1工程分増えるので、リードタイムは長くなってしまうというデメリットもあります。
下図は、SCM435の材質にクロス穴Φ2.0でバリ取りフリーを実現した事例です。
ピアス抜き加工
最後3つ目は、ピアス抜き加工です。機械加工+プレス抜き加工でバリ取りフリーを実現する方法です。
プレスにて横穴をあける為、切削や放電加工と比べて短時間で加工が完了するため、高い生産性を実現できます。
下図は、SCM435の材質にクロス穴Φ1.15でバリ取りフリーを実現した事例です。
クロス穴あけ バリ取りフリーのことなら量産自動盤加工.comにお任せください!
今回は、「クロス穴あけにおけるバリ取りフリー」についてご紹介いたしました。当社では、その穴あけ材質など条件により3通りの方法を使い分けています。
当社では、デンソーなどメガサプライヤーとの自動車部品に関する試作開発を毎年行っており、高い技術力を有しています。
クロス穴あけにおけるバリ取りフリー加工のご要望がございましたら、お気軽にご相談ください。